Progressive Presses
Although we have standard products in two connecting rod and four connecting rod configurations, we produce eccentric presses up to 1000 tons in a single connecting rod.
It is communicated over profinet with sheet feeding system.
In industrial standards, PLC, operator panel, cam case, clutch brake valve, clutch brake, encoder and light barriers are selected from globally accepted brands.
All of our presses are hydraulically fused and have regulation adjustment.
Our presses are PLC controlled. We use safety PLC or safety modules in accordance with 2006/42/EC regulation. Depending on the size of the press, we use 9” or 12” rotary console operator panels.
Prescription-based press speed adjustment and regulation adjustment can be made with the encoder from the operator panel.
We manufacture our presses with fixed or mobile plate and cushioning according to your request.
Our gears are zero-gap herringbone gears.
Body Structure
In progressive presses, mono-block body or tension shaft body can be preferred.
In both body structures, we design by considering the maximum deflection 0.12 mm/m.
The tonnage to be applied in each station of the progressive mould is a critical input in terms of body, ram and sled design.
We design the nuts in the tensioner shaft structure with hydraulic self-tensioning. It ensures that it can be disassembled by applying pressure without the need for additional equipment. It provides convenience for transportation and maintenance.
The side clearance between the columns is determined by the width of the roll to be fed. The position of the columns is one of the criteria determining the whole body structure.
Tonnage and table size determine the press pit requirement
Body design and Manufacturing
Body design is analyzed with Ansys finite element software. In the analysis, we maintain design improvements until we achieve an infinite fatigue life.
We report the results obtained and maintain them by documenting them.
The body is obtained by welding St52-3 quality plates. Welding is performed by certified welders using SG3 welding wire.
After welding, the body is placed in the furnace and subjected to stress relieving process.
Mechanism design
The high speed and reasonable course values required in progressive presses are often provided by the slider crank mechanism.
In our presses, we use an eccentric crank-connector system.
The eccentric system from the gear has superior strength and machine life compared to the direct crank mechanism.
Kinematics
During the process, the parameters of velocity, position, and acceleration are optimized within the limits allowed by the mechanism to properly direct the flow occurring in the material.
While aiming the most appropriate movement curve for the process, it is ensured that the forces to be applied to the press limbs and bearings are kept to a minimum.
Power Train Design
By using the results obtained from the mechanism design and kinematic data, the designs of the powertrain are carried out.
Analysis
In our designs, we use the finite element method to estimate how the powertrain behaves. We use ANSYS software for these analyzes we perform in the computer environment.
ANSYS, one of the modern simulation software, contains the finite element method on its basis. It helps us find the weakest point in our designs and make parameter optimization.
Slide Guiding
The ram is guided on the columns from 8 surfaces.
Each plate is precisely adjusted and secured by means of bolts in the x and y directions.
Optimized lubrication channel and precision machined bronze bearings work on steel plates.
Clutch & Brake
Pneumatic or hydraulic clutch type is used.
Depending on the press speed, mechanism and operating conditions, the clutch type is selected.
The required clutch and brake size are calculated according to the transmitted power, torque, tonnage and speed information.
Clutch- The brake is controlled by a double valve control system with monitoring, three-way safety. It is vitally important for occupational safety.
Shut Height Adjustment and Overload Protection
The ram table height adjustment is achieved by the movement of the nuts working on the thrust bolts.
In our presses, the shut height adjustment and overload protection systems are combined in a single body.
In case of a situation exceeding the press limits during any possible mould failure and mass production, the hydraulic overload valve is activated and possible damage is prevented.
Moving Bolster
One of the most important components of the transfer press is the mobile tables. The way to minimize mould fastening and setting time is to use double mobile table presses.
We manufacture electric motor, hydro motor or air motor driven mobile tables.
We place the mobile table lifting cylinders into the lower bridge. In the same way, we position the centering and locking assemblies in the lower bridge.
We also manufacture mobile tables with shaft holes in presses equipped with air-cushion.
2 Direction Moving Bolster
After the mobile table is out of the press, in some cases, the first movement direction must also move vertically.
We solve this need with 8-wheeled mobile tables. Press shop floor remains level again. 4 wheels to work for the second movement direction remain hidden inside in the first stage. When it comes to the direction change zone, it is activated and provides movement.
Opstion : Traveling Clamp
It is an SMED application used for automatic and fast connection of the upper mold to the press ram.
Preston mould retainers provide faster setup.
Each has a capacity of 6-8-10 tons and a 600 mm or 800 mm advance course.
Receives the plate presence/absence information and transmits it to the PLC.
Continuously checks the pressure, completes the missing pressure.
Transmits pressure incomplete status to the PLC as an emergency warning
Standart Progresif Pres Özellikleri
PresModelNumarası | PP300.2211.200 | PP400.2512.250 | PP500.2713.300 | PP600.3015.400 | PP800.3618.500 | PP1000.4020.600 | PP1250.4522.800 | PP1500.5025.900 |
---|---|---|---|---|---|---|---|---|
Tonaj | 300 ton | 400 ton | 500 ton | 600 ton | 800 ton | 1000 ton | 1250 ton | 1500 ton |
Tabla ölçüleri | 2250 x 1125 mm | 2500 x 1250 mm | 2750 x 1375 mm | 3000 x 1500 mm | 3600 x 1800 mm | 4000 x 2000 mm | 4500 x 2250 mm | 5000 x 2500 mm |
Kurs | 200 mm | 250 mm | 300 mm | 400 mm | 500 mm | 600 mm | 800 mm | 900 mm |
Pres hızı | 15-35 spm | 15-35 spm | 15-35 spm | 15-35 spm | 15-25 spm | 15-25 spm | 15-25 spm | 15-25 spm |
Maks. kalıp bağlama yüksekliği (SDAU) | 650 mm | 650 mm | 700 mm | 700 mm | 800 mm | 900 mm | 1100 mm | 1100 mm |
Reglaj | 200 mm | 200 mm | 200 mm | 250 mm | 250 mm | 250 mm | 300 mm | 300 mm |
Biyel sayısı | 2 adet | 2 adet | 2 adet | 2 adet | 4 adet | 4 adet | 4 adet | 4 adet |
Tonaj anma ölçüsü | 4,5 mm | 5 mm | 5,5 mm | 6 mm | 7,2 mm | 8 mm | 9 mm | 10 mm |
Hidrolik sigorta (HOLP) | var | var | var | var | var | var | var | var |
Mobil tabla | opsiyon | opsiyon | opsiyon | opsiyon | opsiyon | opsiyon | opsiyon | opsiyon |
Kavrama fren | Desch / Ompi | Desch / Ompi | Desch / Ompi | Desch / Ompi | Desch / Ompi | Desch / Ompi | Desch / Ompi | Desch / Ompi |
Standart Progresif Pres Ölçüleri
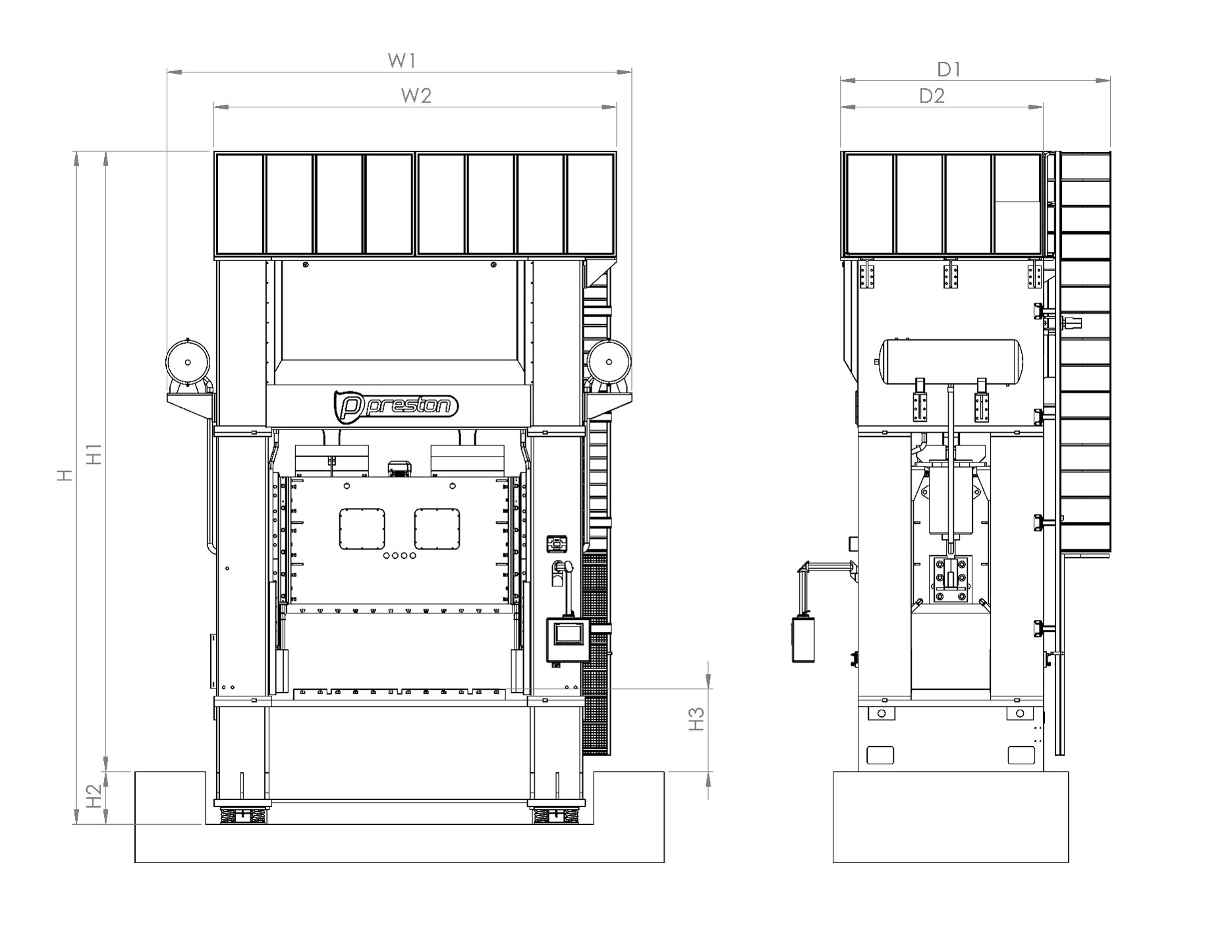
ProgresifPresler | PP300.2211.200 | PP400.2512.250 | PP500.2713.300 | PP600.3015.400 | PP800.3618.500 | PP1000.4020.600 | PP1250.4522.800 | PP1500.5025.900 |
---|---|---|---|---|---|---|---|---|
H | 6750 mm | 6750 mm | 7500 mm | 7900 mm | 8450 mm | 9000 mm | 9870 mm | 10200 mm |
H1 | 6500 mm | 6500 mm | 7000 mm | 7250 mm | 7700 mm | 8100 mm | 8620 mm | 8900 mm |
H2 | 250 mm | 250 mm | 500 mm | 650 mm | 750 mm | 900 mm | 1250 mm | 1300 mm |
H3 | 900 mm | 900 mm | 1000 mm | 1100 mm | 1100 mm | 1100 mm | 1100 mm | 1100 mm |
W1 | 5200 mm | 5450 mm | 5700 mm | 6450 mm | 7600 mm | 8300 mm | 9400 mm | 9400 mm |
W2 | 4500 mm | 4750 mm | 5000 mm | 5750 mm | 6900 mm | 7600 mm | 8700 mm | 8700 mm |
D1 | 3100 mm | 3200 mm | 3300 mm | 3650 mm | 4200 mm | 4900 mm | 5400 mm | 5700 mm |
D2 | 2300 mm | 2400 mm | 2500 mm | 2850 mm | 3400 mm | 4100 mm | 4600 mm | 4900 mm |